CNC (Computer Numerical Control) machining and 3D printing are both popular methods of manufacturing parts, but which one is better? We often get asked this question, so we’ll try to break it down and help make the decision a little more simple by starting with understanding the differences.
What is CNC machining and 3D printing?
CNC machining takes a piece of material – commonly referred to as a blank – and uses any number of machine processes to cut, shave, drill, burr away at this blank until it becomes a finished component. Guided by computer programmed instructions, CNC machines can produce highly accurate and precise parts with smooth surfaces and tight tolerances.
On the other hand, 3D printing involves building up a three-dimensional object layer by layer using a digital model. The process starts with a digital 3D model that is sliced into layers and then printed using a variety of materials, such as plastics, metals, or ceramics. 3D printing can produce complex geometries and shapes that may be difficult or impossible to create with CNC machining. With the industry projected to grow to $50.8B By 2030, it’s clear that 3D printing will only go from strength to strength.
​​As you read on, bear in mind that CNC is a subtractive process while 3D printing is additive. Each more or less begins its lifecycle at opposite ends of the manufacturing spectrum, yet when complete tend to finish in the same spot in the middle of this spectrum.
How does CNC machining work?
When making components using CNC, one or more software-driven machines process a piece of material (normally a steel or other metal, but sometimes a polymer or wood) according to coded, programmed instructions and do so without a manual operator directly controlling the machining operation.
The machines cover nearly every process required by industry including milling, grinding, turning, boring and reaming. Some machines can perform more than one process, but in general the types of machines used include milling machines, lathes, drills, laser cutters, grinders, water jet cutters and plasma cutters.
While the list is quite extensive, we’ll take a look at the most commonly used materials in CNC machining.
Aluminium
Aluminium alloys are easy to machine in large volumes, have a good strength-to-weight ratio, and high thermal and electrical conductivity. They are suitable for machining of auto parts, industrial machines, aircraft components, and various other applications.
Stainless steel
Stainless steel is strong and resistant to distortion, wear, and corrosion. It is used to make bolts, nuts, gears, fittings, kitchen accessories, utensils, tanks, pipes and more.
Carbon steel.
Carbon steel is machined much of the time to create precision instrument parts and important parts for various types of machinery (including shafts, fasteners, manifolds).
Titanium
Titanium is prominent in the biomedical industry. If you are wondering from where all those artificial hips and knees originate, it could be a CNC machine.
Plastics
CNC machines aren’t solely for metals. Plastics feature commonly in machining for decorative parts, toys, complex plastic fittings, plastic furniture fittings, etc.
How does 3D printing work?
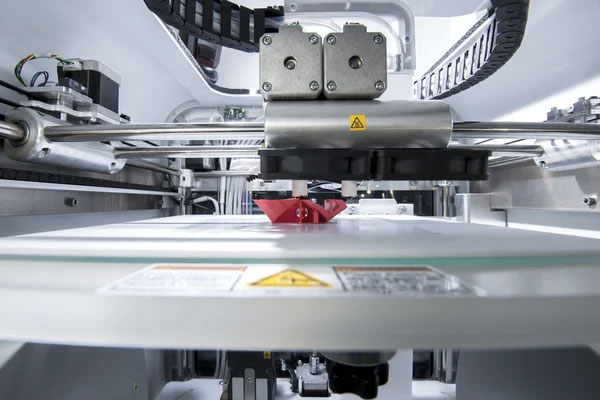
3D printing emerged in the mid-80s as an innovative way to create simplified plastic mock-ups to size or scale but it has really picked up momentum in recent years. Objects are created sequentially layer-by-layer using materials such as plastic filaments (FDM), resins (SLA/DLP), plastic or metal powders (SLS/DMLS/SLM). This is why it is called an ‘additive’ process.
In the last four decades, this option has advanced technologically to the point that 3D printing can deliver quickly in large volumes and in an array of materials – including metals – and is now a common option for supply chain fabricators feeding into aerospace and medical, mechanical engineering and robotics, automotive and tool making.
Plastics are some of the most commonly used materials for 3D printing. They are relatively inexpensive, easy to print, and come in a wide range of colours. They are ideal for prototyping and producing low-cost, low-stress parts. If the components you need are to be made of any type of polymer or plastic, 3D printing is most likely the solution, but never leave it to guesswork – speak with someone that has made this choice before.
Is CNC or 3D printing better for small batches?
If your next challenge is a project involving small batch numbers, 3D printing saves money over hard tooling in producing minimum viable products, which can reduce the upfront costs of producing smaller batches. It is even now exceeding quality and output returns in jobs that traditionally were manufactured by injection moulding – 3D printing can be very cost-effective for the first 200 to 20,000 parts.
CNC machining, on the other hand, is a subtractive manufacturing process that involves cutting material from a larger block to create a part. While CNC machining can produce highly accurate and precise parts, it is typically better suited for high-volume production runs and parts that require tight tolerances. The upfront costs of CNC machining can be higher than 3D printing, particularly for smaller batches, due to the need for tooling and fixtures.
Overall, if you are looking to produce smaller batches of parts with complex geometries, 3D printing may be a better option than CNC machining. However, if you require high precision and tight tolerances, or need to produce large volumes of parts, CNC machining may be the better choice.
Comparing CNC to 3D printing
Equipment and set-up costs
These costs include installation and set-up time, running costs, periodic servicing for machines and more ad-hoc maintenance. As we mentioned, CNC has a higher upfront cost than 3D printing, which makes it better suited to large-scale production volumes over small quantities. The cost of 3D printing can increase significantly for larger production runs or when using higher-end 3D printers that can produce parts with greater precision and accuracy.
Materials each option can process
Technically, all materials (except wood) can be worked by both CNC and 3D printing. Again, quantities and base materials determine the most suitable process. 3D tends to work better with plastics, although modern technologies are making it more efficient when working with metals, ceramics and other materials.
Finishes
CNC machines mostly produce smoother surfaces than 3D printers. 3D printers are capable of producing parts for fit and finish, and can do so cost-efficiently in very small quantities. Generally, keep it in mind that when you are required to fabricate parts with top-level smoothness that fit into other precision components, CNC machining may be the better choice.
Conclusion
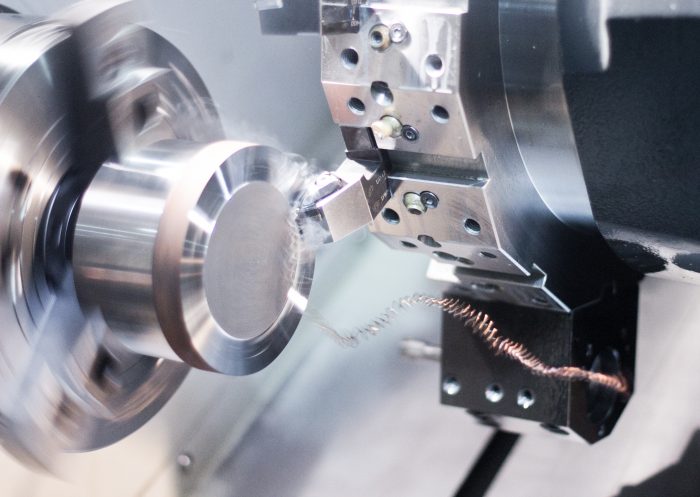
The choice between CNC machining and 3D printing largely depends on the specific requirements of the project. CNC machining is typically faster and more precise than 3D printing, making it better suited for high-volume production runs and parts that require tight tolerances. However, 3D printing can be a more cost-effective and flexible option for smaller runs or complex geometries that are difficult to achieve with traditional manufacturing methods.
CNC machining and 3D printing are both valuable manufacturing methods, each with its own strengths and weaknesses. Choosing between the two methods ultimately depends on the specific needs of the project, including cost, volume, design complexity and viable return.
For any help on choosing between the two, it’s always best to talk to an experienced industry professional such as Elite CNC. Our CNC machining specialists can help you make an informed decision.